From its early days as Astroturf® to the sophisticated synthetic grass we see today, artificial turf history and evolution have been nothing short of remarkable. Advancements in materials, manufacturing technology, and environmental considerations have turned synthetic grass into a sustainable, versatile, and safe option for a wide range of applications.
As we look to the future, the possibilities for artificial turf technology are limitless, promising even more exciting developments in the years to come. Whether it’s for sports, landscaping, or residential use, artificial turf has truly transformed our green spaces.
Today, artificial turf systems are highly advanced and versatile, offering a range of benefits. This is especially apparent when comparing artificial grass vs. natural grass. Synthetic turf systems are durable, require minimal maintenance, and can withstand heavy use. Artificial turf is also more resistant to weather conditions, making it an ideal choice for sports fields, playgrounds, and other outdoor areas.
Despite its widespread use, artificial turf has also faced criticism, particularly regarding its environmental impact and potential health risks. However, ongoing research and development are addressing these concerns, with the introduction of more eco-friendly materials and improved manufacturing processes.
Artificial turf has come a long way since its inception, revolutionizing the way we think about green spaces. In this article, we will delve into the remarkable journey of artificial turf, exploring its early beginnings, the advancements in materials and manufacturing technology, and its impact on various industries.
Artificial Turf History: Early Beginnings of Synthetic Grass
The common belief that synthetic grass was developed specifically for the Houston Astrodome in 1965 is a misconception. To understand the full story, we need to look back further. Originally created to replace concrete and brick, synthetic grass was intended to bring green spaces to city schoolyards.
During the Korean War, the U.S. Army observed that urban recruits were less physically fit than their rural counterparts, and identified the lack of green areas as a potential cause. The Ford Foundation funded research by Monsanto to develop a synthetic grass replica in 1962, aiming for a wear-resistant, cost-efficient, cushioned, and traction-tested surface. Two years later, employees from the Chemstrand Company, a subsidiary of Monsanto, fulfilled this ambition by introducing “ChemGrass.”
This innovative synthetic surface was first installed at the Moses Brown School in Providence, Rhode Island. While the new product met all the original criteria outlined by the Ford Foundation, it was expensive to produce, making it unsuitable for inner-city playgrounds. However, this setback led to a new beginning for the product and a fresh name. Keep reading to learn how AstroTurf® revolutionized the world of sports, offering a durable and comfortable alternative to traditional surfaces.
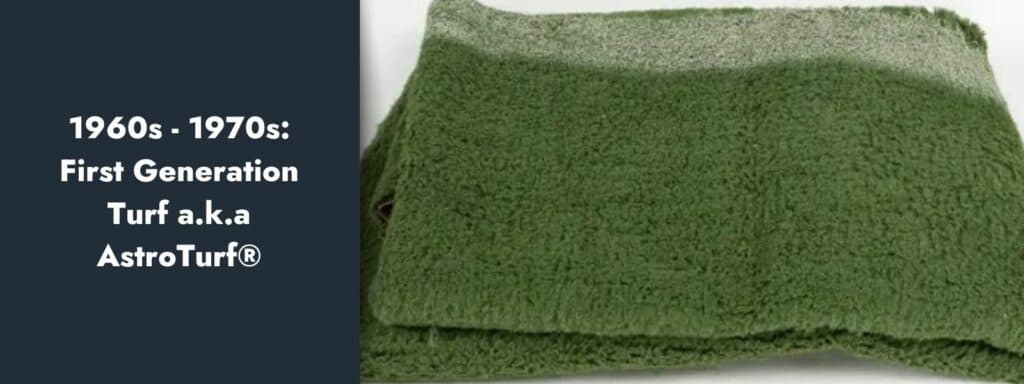
1960s – 1970s: First-Generation Turf a.k.a. Astroturf
In 1965, the Houston Astrodome made history as the first domed stadium with a glass-covered roof, allowing real grass to grow inside. However, the glass caused a glare that made it difficult for athletes to track the ball. Attempts to paint the glass resulted in the grass dying.
In 1966, Houston introduced ChemGrass, later known as AstroTurf®, as a solution. The initial iteration, was far from the lush, realistic surfaces we see today. Astroturf was made from coarse nylon fibers, offering durability but lacking the natural look and feel of real grass.
The drive behind the development of early artificial turf was the need for a low-maintenance, all-weather playing surface for sports. It was a response to the limitations of natural grass, which required extensive care, suffered from wear and tear, and became unusable in inclement weather. Astroturf, although not perfect, provided a significant improvement in these areas. However, its abrasive texture led to concerns about athlete injuries.
This artificial turf revolutionized sports and became popular in stadiums worldwide. Despite its initial drawbacks, AstroTurf® has provided a durable and consistent playing surface for athletes, hosting numerous iconic sporting events, such as:
- 12 World Series
- 11 Super Bowls
- 10 Olympics
- 8 Major League All-Star Games
- 32 NFL Pro Bowls
It has become the preferred surface for stadiums worldwide. However, the first generation of artificial turf posed challenges such as joint problems, player injuries, and material deterioration. Over the years, advancements have been made to improve artificial turf for better performance and player safety.
Astroturf marked the birth of synthetic grass and served as the foundation for future developments. Its introduction brought about a significant shift in sports facility management, allowing for year-round play. However, it had its drawbacks, including a hard and abrasive texture that led to increased injuries among athletes.
Over time, the desire for a more natural look and feel, as well as enhanced safety, drove further innovations in the world of artificial turf. The influence of athlete feedback, coupled with advances in materials and manufacturing technology, played a crucial role in shaping artificial turf history and the ongoing evolution of synthetic grass.
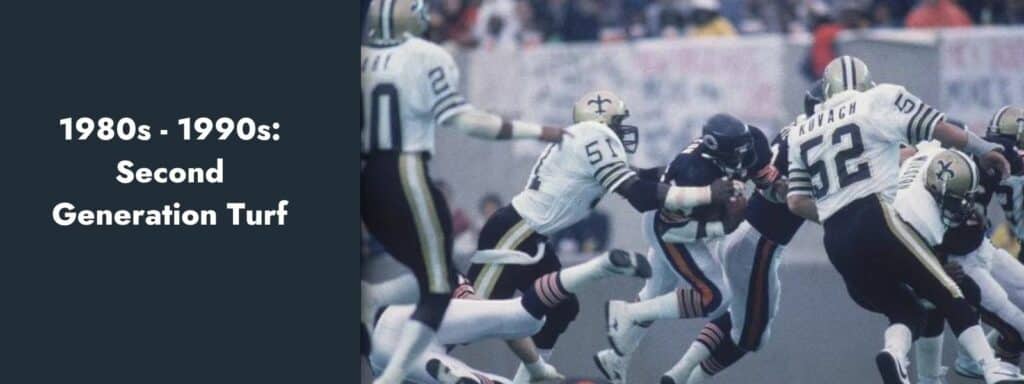
1980s – 1990s: Second-Generation Turf
The second-generation synthetic turf was first invented in 1976 by Frederick T. Haas. The 1980s and 1990s were a time of significant technological progress in the artificial turf industry. With increasing demands for better performance and player safety, manufacturers began creating more advanced turf systems. These surfaces included a shock-absorbing pad beneath a carpet with much longer fibers compared to the first-generation systems.
One important development during this period was the introduction of infill systems. Instead of relying solely on the turf itself for cushioning and support, an infill material was added. The carpet pile was filled with silica sand, which filled the spaces between the turf fibers, allowing them to stand upright. This innovation greatly improved shock absorption, reducing the risk of player injuries, particularly in high-impact sports like football.
Additionally, the materials used in artificial turf underwent significant enhancements. Second-generation turf systems featured longer and softer fibers, making the playing surface even more similar to natural grass.
While this second-generation artificial turf worked well for sports like field hockey, it did not replicate the behavior of natural grass for football, baseball, and lacrosse. Not only did the ball not behave “right,” but it also caused painful abrasion injuries from the sand. In the early 1990s, many sports stadiums switched back to natural grass playing fields. However, issues persisted with natural fields, such as challenging maintenance and the need for abundant sunlight.
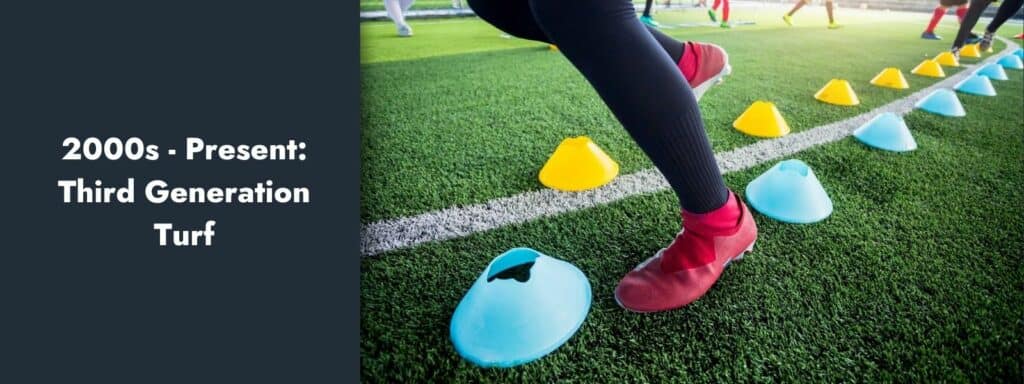
2000s – Present: Third-Generation Turf
Third-generation turf surfaces involve filling the space between vertical pile fibers with a granular material, creating an infilled system. These systems use infill materials such as crumb rubber or a combination of crumb rubber and silica sand, unlike the pure sand used in second-generation systems. The initial third-generation system was created by FieldTurf and was first installed in 1997 at a Pennsylvania high school. Subsequently, multiple companies have produced similar products.
The most recent iteration of sports turfs provides an exceptional playing surface that exceeds all previous versions. Thanks to revolutionary advancements in materials, artificial grass blades have become softer and less abrasive. Combined with high-performance backing materials, these modern sports turfs are specifically engineered to meet the unique requirements of every major sport.
Third-generation artificial turf fields now provide improved safety, playability, appearance, and durability, with lower operating costs and reduced annual maintenance needs. These fields are used more frequently than natural grass fields due to their lower maintenance requirements, making them suitable for use even in unfavorable weather conditions.
Maintaining synthetic grass is easy, which is why many universities and professional teams are opting to install it once again. The new, 3rd generation sports turf brings significant enhancements. The grass blades are taller and spaced farther apart, allowing players to dig their cleats deeper into the turf. This reduces strain on joints and gives athletes better traction and performance.
Furthermore, the use of polyethylene instead of polypropylene has resulted in softer and less abrasive blades. Tackles can now be executed comfortably, without the concern of skin abrasion. With the introduction of these advanced sports turfs, athletes can now play at higher speeds with reduced risk of injury.
Now that we’re caught up on artificial turf history and how it has evolved over the years, let’s drill down further. Below, we’ll explore the advancements in materials, technologies, and manufacturing processes. We’ll also provide an overview of the components and features that make modern synthetic grass possible.
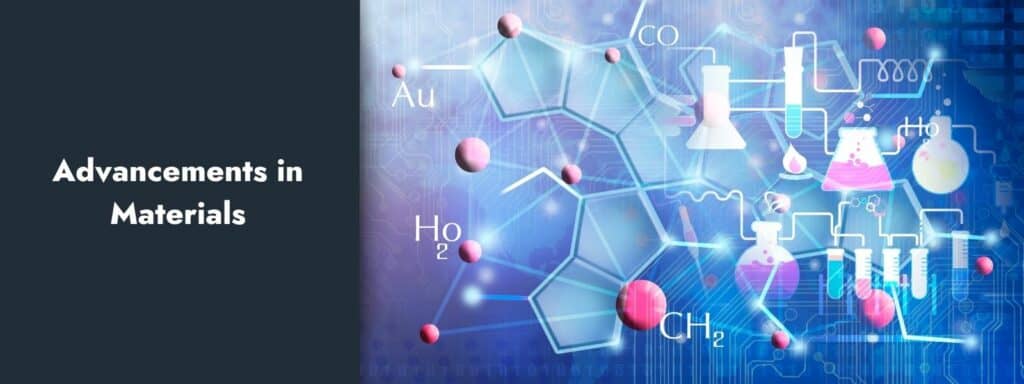
Advancements in Materials
One of the key drivers behind the evolution of artificial turf has been the continuous improvement of materials used in its construction. Over the years, synthetic grass has seen remarkable advancements in materials, leading to improved performance and aesthetics. Beginning with short, dense nylon fibers that were less than 0.05” (<1.25mm), the original iterations of artificial turf left a lot to be desired.
Advancements in technology, design, and manufacturing have resulted in artificial turf with less dense and much longer fibers. Composed of Polyethylene, Polypropylene, or Nylon, modern turf fibers can range from 0.5” (13mm) to 2.75” (70mm) or more. The increased space between fibers allows for the inclusion of granular infill materials like crumb rubber and sand. It’s a combination of longer fibers, granular infill materials, and impact-absorbing shock pads that helped to create modern turf products.
Nylon
Nylon fibers added versatility to artificial turf. Known for their strength and resilience, nylon fibers are commonly used in sports fields, ensuring the turf can withstand the demands of various sports and activities. The influence here was to create a turf that could accommodate a wide range of sports without compromising performance.
Polypropylene
Polypropylene fibers brought enhanced durability to artificial turf. They are resistant to wear and tear, making synthetic grass a long-lasting choice for high-traffic areas. This development was driven by the need for longevity, especially in sports fields that faced heavy use. The influence of maintaining performance over time was a driving force behind the use of polypropylene. With the introduction of Polyethylene, Polypropylene became the go-to material for Thatch Fibers.
Polyethylene
The introduction of polyethylene fibers revolutionized artificial turf, as they provided a softer, more natural appearance and feel. Polyethylene mimics the texture of real grass blades, enhancing the overall look and comfort of synthetic turf surfaces. This shift was largely influenced by the desire to create a more lifelike alternative to natural grass. The true-to-life look and feel of Polyethylene turf fibers made it much more appealing for residential applications.
Advancements in Manufacturing Technology
Technological innovations have played a pivotal role in shaping the manufacturing process, or how synthetic turf is made. These advancements have made the production of artificial grass more efficient and consistent.
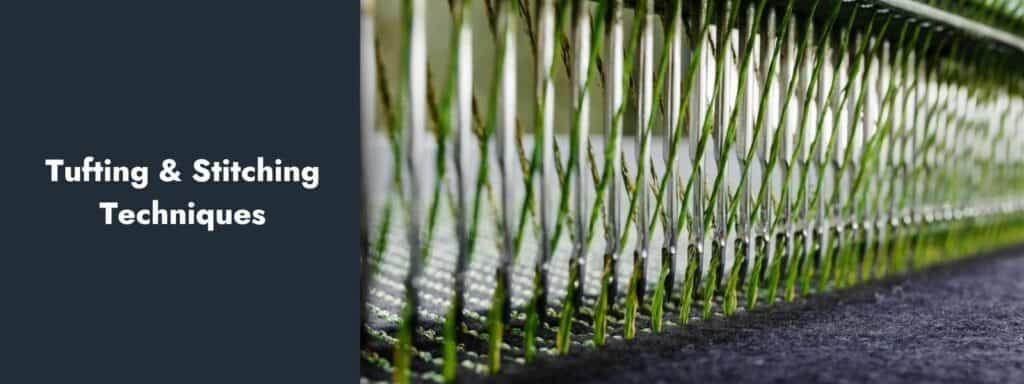
Tufting & Stitching Techniques
The improvement of tufting and stitching techniques has significantly enhanced the production of artificial turf. Tufting involves the insertion of synthetic grass fibers into a backing material to create a turf’s surface. Advances in this technique have allowed for more precise placement of fibers, resulting in a seamless and natural appearance.
Computer-controlled machinery plays a crucial role in this aspect by ensuring consistent spacing and alignment of the fibers. It has revolutionized the manufacturing process of artificial turf, offering several advantages, including increased speed and precision. Stitching techniques, which are responsible for securing the turf fibers to the backing, have also evolved.
These techniques have become more sophisticated, ensuring that the fibers remain firmly attached, even under heavy use. Overall, the refinement of tufting and stitching methods has improved the overall quality and aesthetics of artificial turf, making it virtually indistinguishable from natural grass.
Automated systems can tuft and stitch fibers at a much faster rate than manual labor, leading to higher production efficiency. Moreover, computer control ensures consistency in fiber placement, density, and alignment, resulting in a more uniform and visually appealing surface. This level of precision is especially critical for sports fields, where consistent playing conditions are essential.
Additionally, computer-controlled machinery allows for customization, enabling manufacturers to tailor turf designs to meet specific performance requirements for different sports and applications. The integration of computer technology has streamlined the manufacturing of artificial turf, resulting in higher quality and more versatile products.
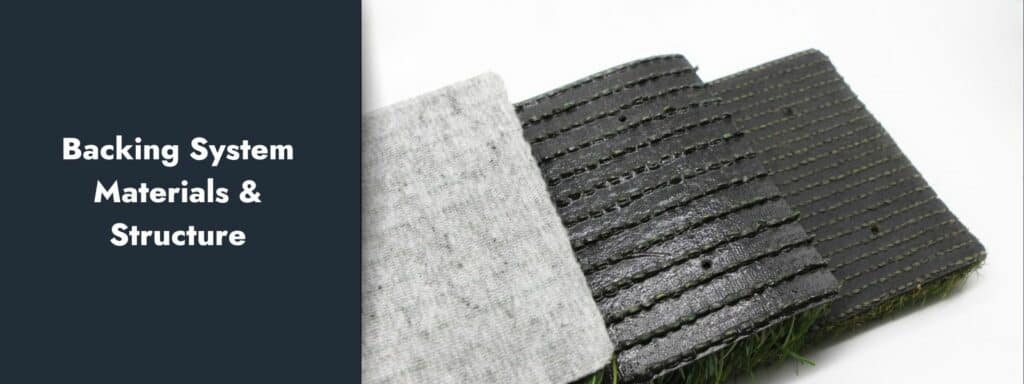
Backing System Materials & Structure
The backing of artificial grass is essential for maintaining the stability, durability, and overall quality of synthetic turf. It plays a crucial role in keeping the grass blades securely in place, preventing them from being pulled out, and providing strength and longevity to the artificial grass. Choosing a high-quality backing with sufficient latex or polyurethane content ensures a resilient and durable turf that can withstand yarn loss, thinning, breaking, cracking, and layer separation over time.
The low-quality backing found on first and second-generation turf products led to various issues. Turf backings were often simple and non-permeable, lacking the ability to efficiently manage water drainage. Yarn loss and thinning of the turf fibers had become common problems.
Since then, the backing systems of artificial turf have seen significant improvements and have undergone a transformation to address these limitations. They now incorporate multiple layers, each serving a specific purpose, and are designed to provide enhanced stability, drainage, and overall performance.
Modern turf backing systems typically consist of multiple layers, including a primary backing, a secondary backing, and sometimes additional layers for specific functions. These reinforcement layers provide added strength and durability. The backing systems of modern artificial turf products offer several benefits, including improved water drainage, better stability, and enhanced longevity. They are capable of withstanding heavy use and adverse weather conditions, making artificial turf suitable for various applications, from sports fields to landscaping, and contributing to a more sustainable and resilient surface.
Primary Backing:
The primary backing provides the initial stability by holding the turf fibers in place. It consists of woven or non-woven fabric made from high-strength polyester or polypropylene. The primary backing provides a foundation for the synthetic grass fibers to be tufted into rows and facilitates seaming between panels. Three common types of primary backing include:
- One layer of polypropylene fabric + One layer of net fabric
- One layer of polypropylene fabric + One layer of non-woven fabric
- Two layers of polypropylene fabrics
Secondary Backing:
The secondary backing is applied to permanently secure the tufts and enhance the stability of the artificial turf system. The most commonly used coating material here in the U.S. is polyurethane. In Europe and Asia, Latex is more common as the coating material on turf backings. Some manufacturers may attempt to reduce costs by decreasing the amount of latex or polyurethane in the secondary layer of the backing, but this compromises the strength and lifespan of the turf.
Latex Coated Backing
The difficult nature of sourcing natural latex led to the creation of synthetic latex, a man-made compound designed to mimic the properties of natural latex. Instead of originating from rubber trees, synthetic latex is made from petrochemicals. The most commonly used type in the production of synthetic grass is SBR (styrene-butadiene rubber).
Latex or SBR (Styrene-Butadiene Rubber) coating offers several important features that make it a popular choice for artificial turf backing:
- Durability: Withstands heavy foot traffic and outdoor conditions, ensuring long-term performance.
- Stability: A latex coating securely holds grass fibers in place, maintaining the appearance and functionality of the turf.
- Cost-effectiveness: Latex provides a balance between durability and affordability, making it suitable for various applications.
- Versatility: Latex is compatible with different types of grass fibers and infill materials.
Polyurethane (PU) Coated Backing
Polyurethanes are polymers that consist of interconnected three-dimensional structures made up of repeating monomer units. Other well-known polymers include nylon, silicone, polyethylene, polypropylene, and polystyrene.
Polyurethane has several properties that make it an excellent material for producing synthetic grass. It provides strong bonding, ensuring that the individual grass fibers remain in place and enhancing their durability. Its strength and resilience make it resistant to wear and tear, making it suitable for heavy foot traffic. Additionally, its flexibility simplifies the installation process, not to mention its lightweight nature.
Overall, polyurethane is a versatile material with exceptional qualities that improve the performance and longevity of synthetic grass. Polyurethane is the preferred modern alternative to rubber because it offers greater versatility, strength, flexibility, and durability. It is also resistant to UV rays, chemicals, and water, making it invaluable in outdoor synthetic grass applications.
A polyurethane coating offers several advantages over other materials:
- Flexibility: Polyurethane is highly moldable and flexible, making it ideal for custom synthetic grass projects, especially those with uneven terrain or awkwardly shaped areas.
- Ease of Installation: Since polyurethane is thinner and more manageable than other backing materials, pieces of turf can be cut and adhered to one another much more easily.
- Durability: Compared to other backing materials such as latex or rubber, polyurethane does not crumble or degrade and has consistently performed better in aging tests. A polyurethane backing will help extend the lifespan of your synthetic grass.
- Temperature Resistance: Polyurethane can generally withstand temperatures ranging from –80° F to 200° F without breaking down.
Improvements to the Components & Features of Artificial Turf Systems
As we’ve established, artificial turf history is littered with failed attempts at a realistic and high-performing ground cover for sports. The incremental improvements to the individual components of artificial turf systems have transformed synthetic grass. Originally intended for sports fields, synthetic grass has evolved into a versatile, safe, durable, and long-lasting ground cover.
Third-generation (3G) turf is such an improvement over the first and second generations, that it’s become extremely popular as an alternative to natural grass in countless applications beyond sports fields. From sports fields to dog parks to backyard putting greens to front yard lawns to children’s playgrounds, artificial turf can be installed just about anywhere.
Below we’ll explore the individual components of artificial turf systems as well as the features that have been incorporated into synthetic grass. We’ll see how these improvements have transformed artificial turf from a nylon carpet for sports fields into the marvel of engineering that is modern synthetic grass.
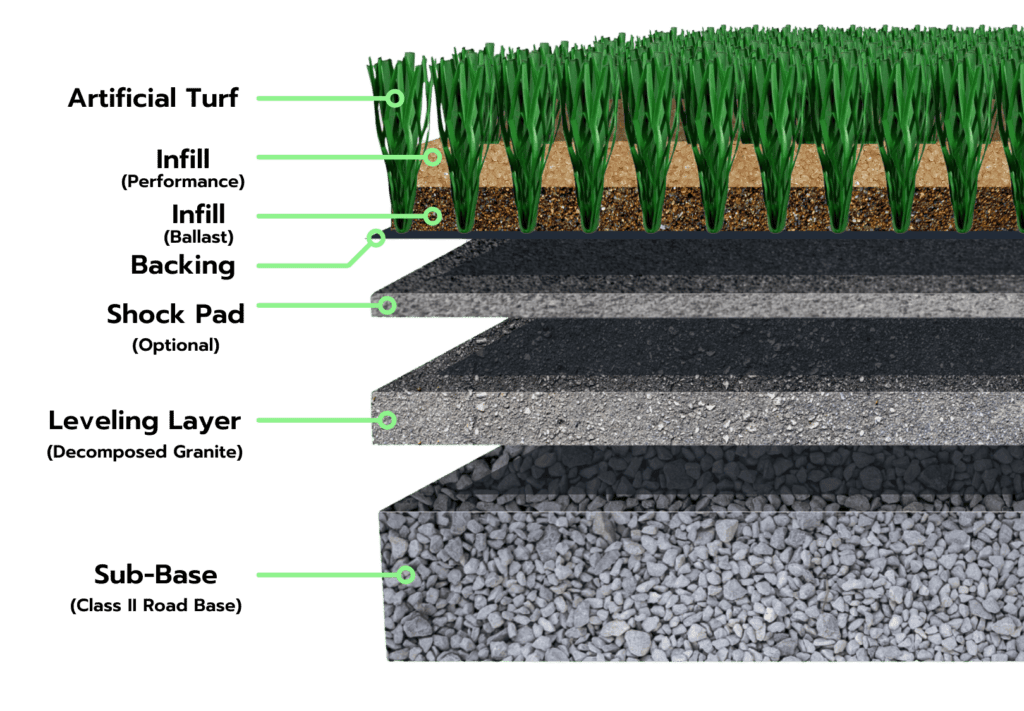
Components
In addition to yarn/fibers, artificial turf components include thatch fibers, backing, infill, and base materials. We’ve also included two optional components, shock pads, and drainage tiles, which help to increase the functionality, versatility, and usability of artificial turf. Improvements to the individual components of artificial turf systems have led to the durable and high-performance systems we see today.
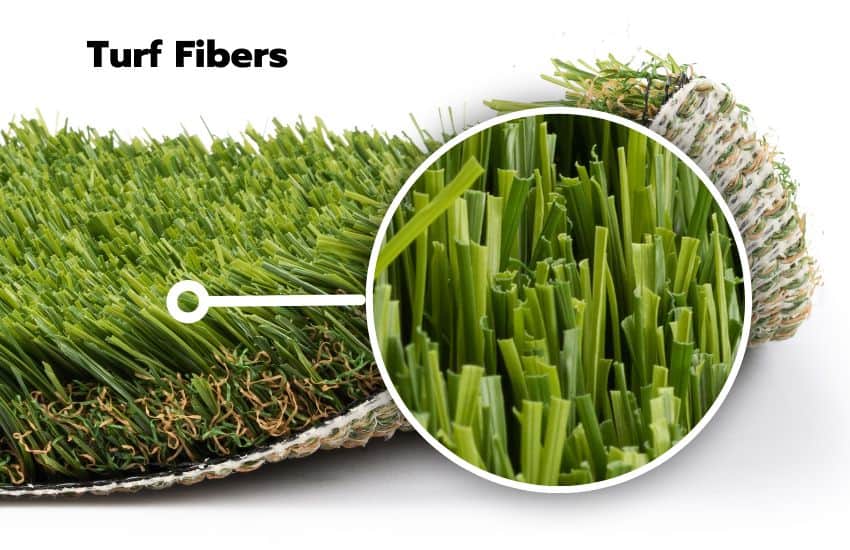
Yarn / Turf Fibers
Artificial turf fibers have undergone significant evolution over the years, driven by advancements in materials and manufacturing technology. With technological progress, materials like polyethylene and polypropylene emerged as game-changers in the synthetic grass industry. Polyethylene fibers, in particular, have transformed the landscape by providing a softer, more realistic texture that mimics natural grass blades. These fibers are often used in monofilament designs, where each strand is a single, uniform filament. Monofilament fibers offer a smoother, more consistent appearance and feel, enhancing the overall aesthetic appeal of artificial turf.
Advancements in manufacturing technology have allowed for the creation of various fiber shapes, including C-shaped and diamond-shaped profiles. These different shapes offer performance benefits such as improved resilience, durability, and recovery. For example, C-shaped fibers provide better “memory,” allowing the blades to bounce back quickly after compression, which is crucial for maintaining the turf’s lush appearance.
Diamond-shaped fibers, on the other hand, enhance resilience and contribute to the turf’s ability to withstand heavy foot traffic, making them popular choices for high-traffic areas and sports fields. Overall, the synergy of improved materials and innovative fiber shapes has led to more realistic and high-performing artificial turf, making it a versatile choice for sports, landscaping, and various other applications.
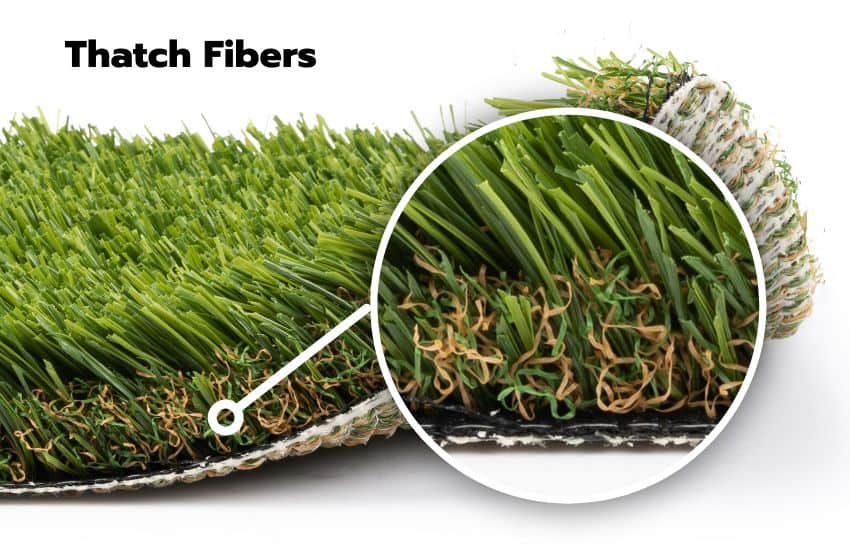
Thatch Fibers
Thatch fibers have been optimized to mimic the natural layer of organic matter found in real grass, providing cushioning and support. Thatch fibers have played a crucial role in improving artificial turf by enhancing its performance and aesthetic qualities.
Thatch is the layer of organic material found in natural grass that provides cushioning and support. In artificial turf, thatch fibers mimic this natural layer, contributing to a more realistic look and feel. Over the years, advancements in thatch fiber technology have resulted in thicker, more resilient layers, improving shock absorption and reducing surface hardness.
This not only makes artificial turf safer for athletes but also creates a more comfortable and enjoyable playing experience. Additionally, the presence of well-designed thatch fibers helps maintain the upright position of the main yarn/fibers, ensuring a lush and upright appearance that closely resembles natural grass. Overall, improvements in thatch fibers have significantly elevated the quality and performance of artificial turf surfaces in sports and landscaping applications.
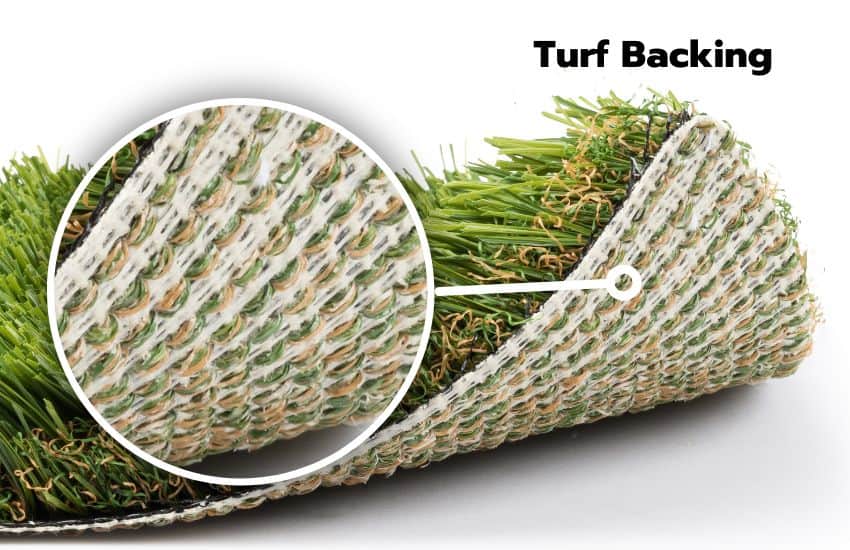
Backing
Backing materials have evolved to include multi-layer systems, enhancing durability and turf drainage. The evolution of the backing on artificial turf has been marked by substantial improvements in both materials and manufacturing technology. In the early days of synthetic grass, backings were typically simple, non-permeable layers that did not facilitate proper drainage. However, advancements in materials have led to the development of hole-punched and fully permeable backings, which have significantly enhanced the performance and functionality of artificial turf.
Hole-punched backings feature strategically placed perforations that allow for better water drainage. This innovation ensures that rainwater or irrigation quickly seeps through the turf, preventing water accumulation on the surface and minimizing the risk of puddling.
Fully permeable backings take drainage to the next level. These backings are designed to be entirely porous, allowing water to pass through freely and efficiently. This not only improves drainage but also contributes to the durability of the turf by preventing water-related damage. Overall, the transition from non-permeable to hole-punched and fully-permeable backings has been a significant advancement, making modern artificial turf more resilient, safer, and suitable for sports fields, landscaping, recreational spaces, and more.
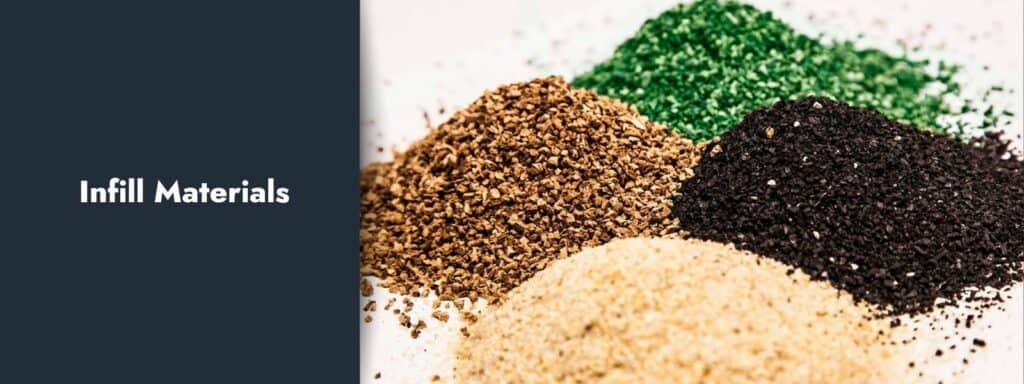
Infill Materials
The evolution of infill materials for artificial turf has been shaped by improvements in both materials and manufacturing technology, leading to enhanced performance, safety, and sustainability. Infill materials serve crucial roles in artificial turf systems by keeping fibers upright, protecting backing from UV rays, acting as ballast, mimicking the sensation of natural grass, and improving drainage efficiency. Over the years, various types of infill materials have been developed to cater to specific needs and preferences. The following are the more popular and commonly used infill materials:
- Silica Sand Infill
- T°Cool Infill
- Envirofill
- HydroChill
- ZeoLite Infill (ZeoFill)
- BrockFILL™
- EPDM Infill
- Cork Infill
- Walnut Shell Infill
- Crumb Rubber Infill
Traditionally, sand was a common infill choice, offering stability and support. However, it lacked cushioning properties and could become compacted over time. Rubber infill, made from recycled tire rubber, addressed these issues by providing shock absorption, making it particularly popular for sports fields. Acrylic-coated sand combines the stability of sand with the cushioning of rubber, offering a balanced solution. It prevents the rubber from migrating while maintaining optimal performance.
Furthermore, advancements in manufacturing technology have led to more sustainable infill options. Eco-friendly infill materials, such as cork and coconut fibers, have gained popularity due to their natural origin and biodegradability. These materials not only provide excellent shock absorption but also reduce the environmental impact of artificial turf systems. In essence, the evolution of infill materials has diversified options, allowing users to choose the infill type that best suits their needs, whether it’s for sports, landscaping, or environmental considerations.
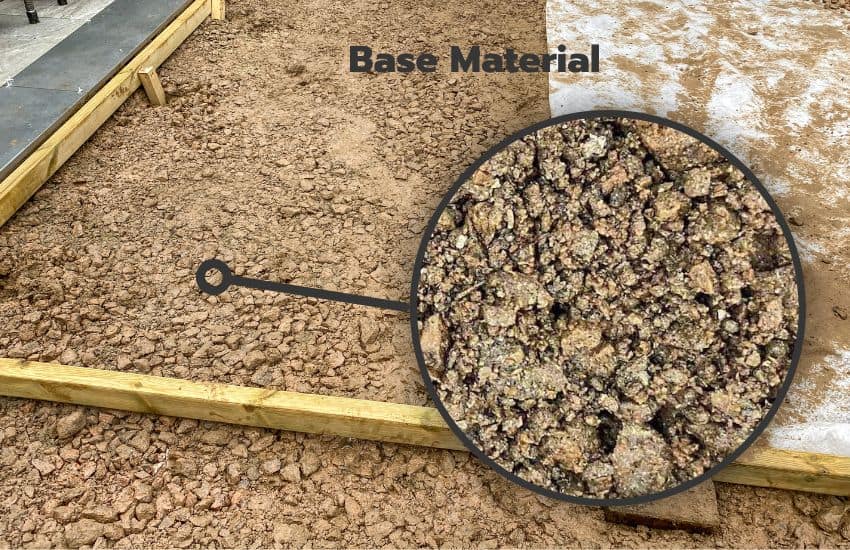
Sub-Base Materials
Sub-base materials for artificial turf have seen significant improvements over the years. This is particularly true in terms of stability, drainage, and environmental considerations. In the early stages of synthetic turf installations, a traditional aggregate sub-base was commonly used, typically consisting of crushed stone or gravel. While effective in providing stability, these materials often had limitations in terms of drainage and environmental impact.
Modern artificial turf installations have witnessed advancements in sub-base materials, with a focus on improved drainage and sustainability. Permeable sub-base systems, incorporating materials like porous aggregates or geo-textiles, have become increasingly popular. These materials allow for efficient water drainage, reducing the risk of water accumulation and creating a more durable playing surface.
The availability and popularity of each sub-base material varies by location. Some sub-base materials are better suited to drier, more arid climates. Others are more effective at efficiently draining water in areas with heavy rainfall or dog urine in pet-friendly applications. To find the best sub-base material for your artificial turf project, speak with a local turf installer or check the artificial turf manufacturer’s recommendations. The most popular sub-base materials for artificial turf are listed below.
- Class II Road Base
- Decomposed Granite
- Crushed Aggregate Base (CAB)
- Crushed Miscellaneous Base (CMB)
- Limestone Chat
Additionally, the use of recycled materials in sub-bases, such as crushed recycled concrete, contributes to sustainability efforts by repurposing existing resources. Overall, the evolution of sub-base materials has resulted in more efficient, environmentally friendly, and long-lasting artificial turf installations, suitable for various residential and commercial applications ranging from sports fields to landscaping.
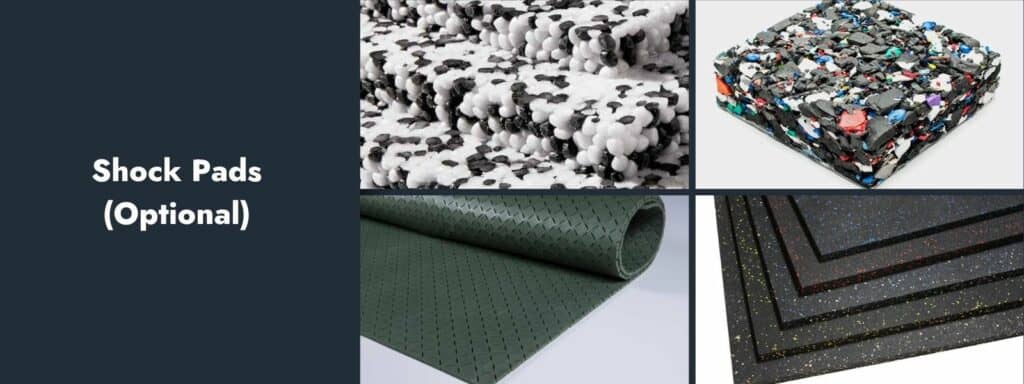
Shock Pads (Optional)
Shock pads or padding in artificial grass installations is a layer of cushioning material placed beneath the artificial turf to improve safety, comfort, and longevity. This padding is especially important in areas where impact absorption is critical, such as playgrounds, children’s play areas, and sports fields. The main purposes of padding in artificial grass installations include:
- Impact Absorption & Safety: Padding offers a soft, cushioned layer that absorbs impact and reduces the risk of injuries from falls, particularly crucial in playgrounds or sports areas.
- Comfort: The additional cushioning from padding makes the artificial turf feel softer and more comfortable underfoot, similar to natural grass, which is beneficial in residential applications or areas where people might walk barefoot.
- Drainage: Some types of padding also assist in turf drainage, allowing water to pass through the turf and padding layer, preventing water accumulation, and speeding up drying after rain.
- Turf Longevity: By providing a protective layer between the turf and the sub-base material, padding can help prolong the life of the artificial grass by reducing wear and tear on the turf backing, especially in high-traffic areas.
Padding materials can vary and may include foam, rubber, or specialized synthetic materials designed for specific uses. The choice of padding depends on the intended use of the area, the desired level of cushioning, and the overall budget for the project. For example, thicker, denser padding might be used in a playground, while less dense padding could be suitable for a residential lawn area.
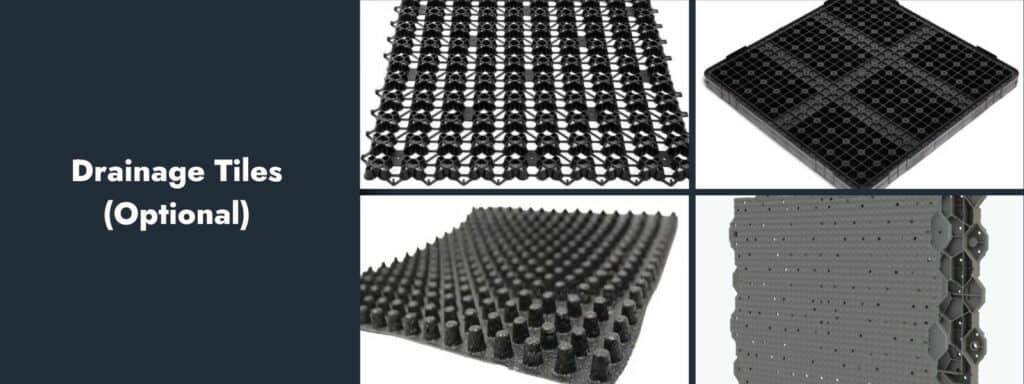
Drainage Tiles (Optional)
Artificial grass drainage tiles are specialized components utilized in the installation of synthetic turf to improve its drainage capabilities. These tiles are crafted to establish a permeable layer between the artificial grass and the sub-base material, facilitating efficient water drainage through the turf. They are particularly beneficial in areas where rapid and effective drainage is crucial, such as in regions with heavy rainfall, concrete surfaces, rooftops, or pet areas.
Drainage tiles are commonly constructed from durable, lightweight plastic or rubber and often feature a grid or channel structure. This design enables water to swiftly flow through the turf and the drainage tiles, where it is then directed away from the area. The use of drainage tiles is essential in preventing water from accumulating on the surface of the turf, which can result in issues like mold, mildew, and deterioration of the turf backing over time.
In addition to improving turf drainage, these tiles can also offer other advantages. They can provide a level of cushioning and shock absorption to the turf, making it safer and more comfortable for activities. Additionally, they can assist in the uniform distribution of the turf, ensuring a more consistent and level surface. Drainage tiles are simple to install and can be a crucial element in ensuring the durability and functionality of a synthetic turf installation, especially in areas with specific drainage requirements.
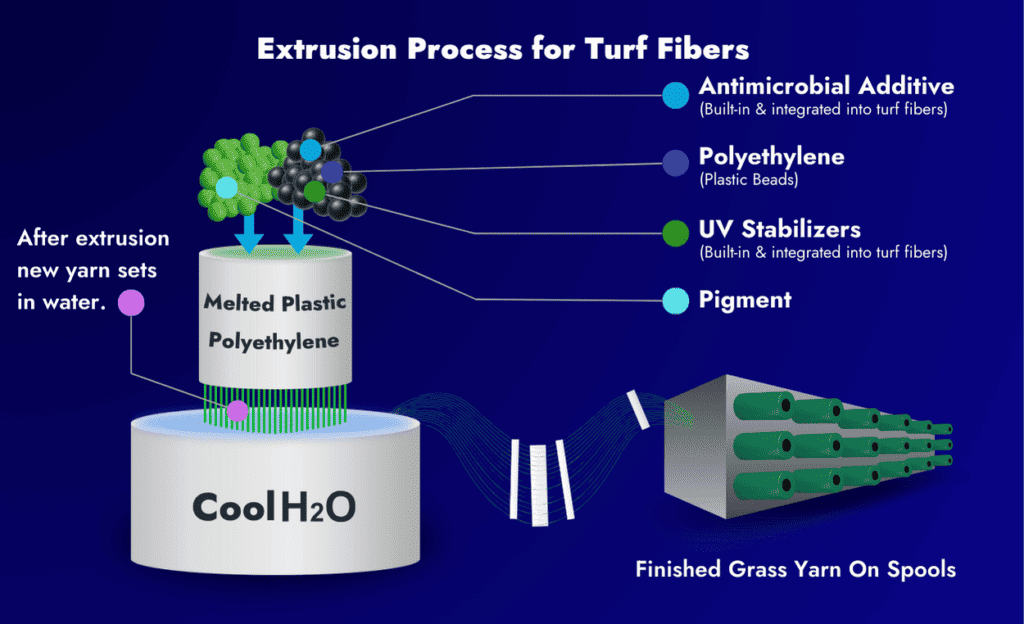
Features
Synthetic grass now incorporates features like antimicrobial protection, UV protection, flow-through drainage, anti-static properties, and more. These features enhance the durability, longevity, safety, and hygiene of artificial turf surfaces. Below, we’ll explore the most impactful features of artificial turf to see how they’ve influenced the evolution of synthetic grass.
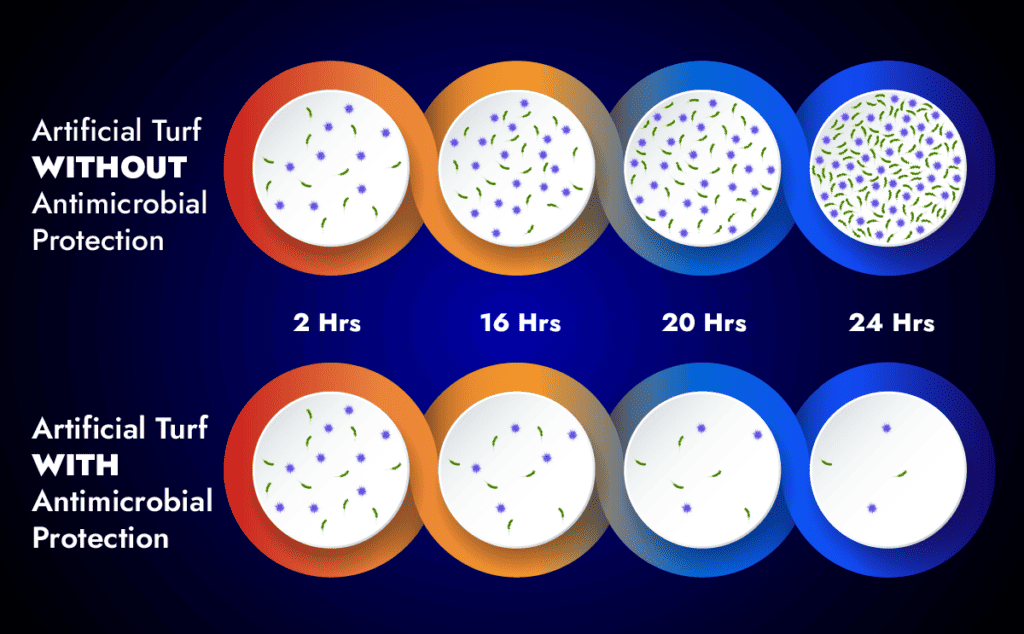
Antimicrobial Protection
Antimicrobial protection has been incorporated into artificial turf through the integration of antimicrobial agents into the turf fibers, backing, or infill materials during the manufacturing process. These antimicrobial additives work by “destroying or inhibiting the growth of microorganisms and especially pathogenic microorganisms.” — Merriam Webster
Antimicrobial technology is infused into artificial grass to eliminate or inhibit the growth and reproduction of bacteria, mold, and mildew. Treating artificial grass with antimicrobial technology can prevent the growth of these unwanted microbes, which can cause unpleasant odors, stains, and even mold or mildew.
The antimicrobial technology is not temporary, like disinfectants. It consistently works to keep the number of microbes low throughout the entire lifespan of the treated product, rather than just temporarily reducing their presence. Because the antimicrobial additives are integrated into the turf, they last for the lifetime of the product, ensuring that artificial grass stays cleaner and fresher for longer. This feature is especially valuable on fake grass for dogs that are used in dog runs and dog potty areas. The antimicrobial protection helps to prevent the buildup of odors, bacteria, mold, mildew, etc.
Antimicrobial protection can be integrated into the backing and fibers of artificial grass, like on some of Foreverlawn’s products (AlphaSan®). It’s also a key feature of popular infill products such as Envirofill and T°Cool™, which are commonly used in pet-friendly applications. T°Cool Infill includes the antimicrobial additive, BacShield, while Envirofill is integrated with Microban® antimicrobial technology. These infill products are equipped with an antimicrobial coating that helps prevent the buildup of odors and bacteria in pet turf installations.
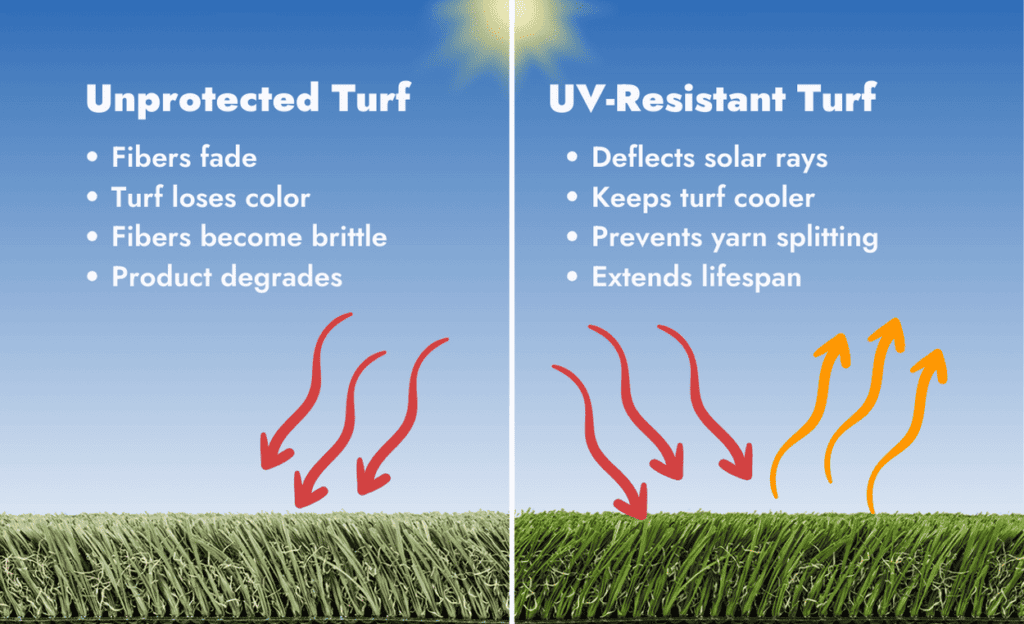
UV Protection
The introduction of UV Protection is one of the most important advancements in artificial turf. UV-resistant synthetic turf refers to artificial grass products that are designed to withstand the damaging effects of the sun’s UV rays. UV resistance is essential for preserving the appearance and durability of synthetic grass. When synthetic turf fibers are exposed to ultraviolet (UV) light, they can undergo discoloration or deterioration. This is due to the process of “photooxidative degradation,” which breaks down polymer chains and ultimately leads to the complete degradation of the material.
To counteract these effects, modern artificial grass products incorporate UV stabilizers. These additives, which are included in the resin before the synthetic blades are formed, protect against UV rays and prevent UV degradation. By integrating the stabilizers directly into the turf fiber and backing material, they become a part of the molecular structure of the turf.
UV stabilizers are integrated into synthetic turf along with other enhancements such as antimicrobial protection. Making these additives a part of the physical structure of the turf ensures that they remain effective throughout the lifespan of the product and do not diminish or wash away. With proper care and maintenance, top-notch artificial grass can retain its vibrant green color for many years, providing a natural-looking landscape for the long term.
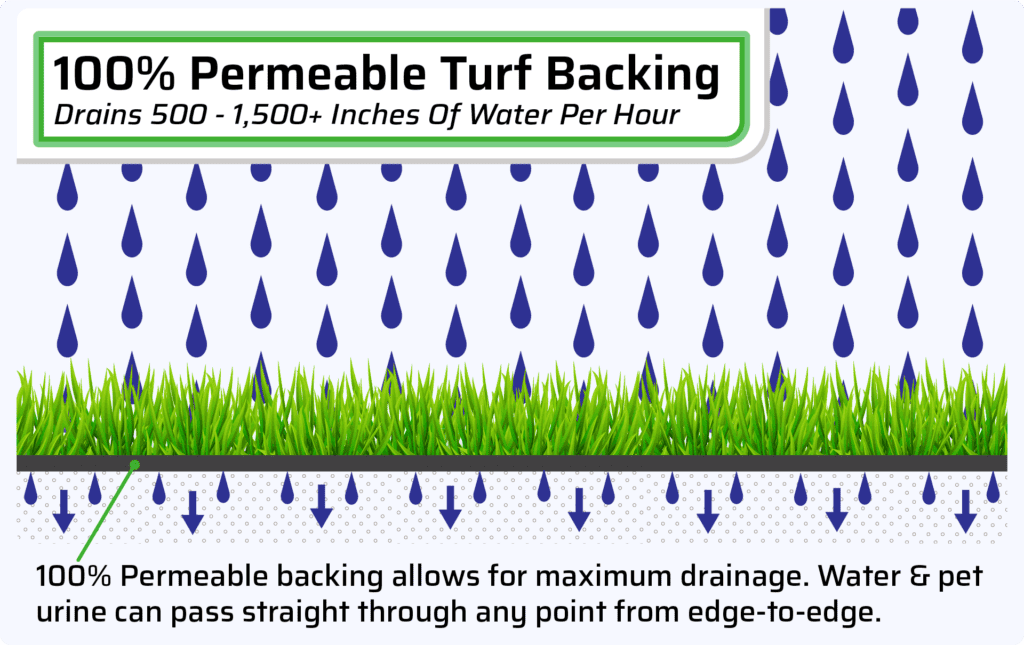
Flow-Through Drainage (100% Permeable)
A specialized backing layer known as fully permeable turf backing is utilized in artificial turf systems to facilitate rapid and efficient drainage of water and liquids. This type of backing is particularly important in areas where effective turf drainage is crucial, such as pet areas, playgrounds, sports fields, and regions with high precipitation.
Fully-permeable turf backings are typically made using a mesh or grid-like pattern of woven or non-woven fabrics, or perforated material, creating numerous channels and pores for water to pass through. This design differs from traditional turf backing, which may have limited perforations for drainage and may be less effective in quickly draining large volumes of water.
The permeable nature of the backing helps prevent water from pooling, reduces the risk of mold and mildew growth, and ensures that the turf surface dries quickly after rain or cleaning. Additionally, fully permeable backings contribute to the overall durability of the turf by maintaining structural integrity and reducing the likelihood of water-induced damage over time.
Modern artificial turf installations incorporate sub-base systems that complement the fully permeable backing, ensuring that excess water is efficiently channeled away from the surface. In installations where fast and effective drainage is a priority, fully permeable turf backing is often the best choice to ensure a functional and long-lasting artificial grass surface.
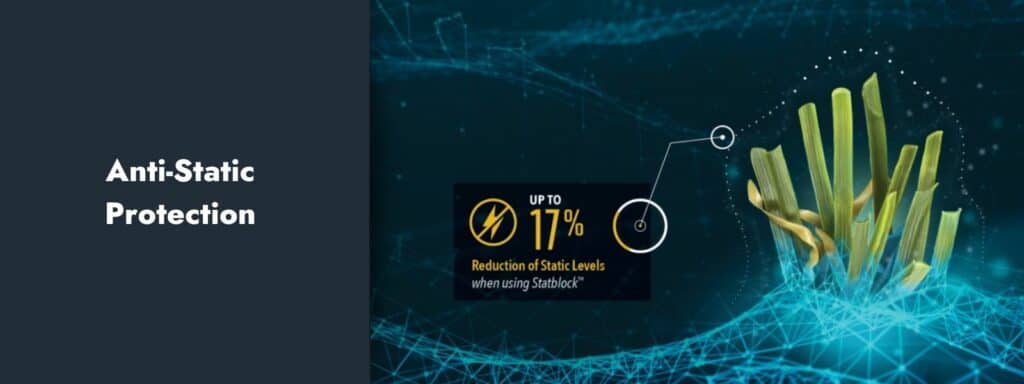
Anti-Static Protection
Static electricity is the buildup of electric charge on an object. It can occur when two objects rub against each other, causing electrons to be transferred from one object to the other. When the charge becomes large enough, it can be discharged in the form of a spark.
Artificial turf can generate static electricity due to the friction between the fibers and the shoes of athletes, children, or other users. This can be a problem because it can cause discomfort to users and can also damage electronic equipment. For kids with cochlear implants or other electronic medical devices, static electricity is a threat to them as it has the potential to damage their much-needed devices.
To reduce the risk of static electricity, artificial turf manufacturers often add anti-static protection to their turf products. ForeverLawn was awarded the industry’s first patent for antistatic turf, namely their “Playground Grass Ultra.” Playground Grass Ultra uses lightly textured polyethylene blades with a textured nylon thatch zone to create a full, dense, and safe product. The fullness comes from the construction, and the additional safety is a result of the AlphaSan® antimicrobial and X-Static® antistatic technology that is manufactured into the blades.
Not to be outdone, SYNLawn has continued pushing the turf industry forward with innovative advancements to its turf products. They introduced “StatBlock™,” a new carbon-based anti-static ingredient molecularly bound into the face fiber that inhibits the buildup of static electricity. Anti-static components are used in the industry but SYNLawn brings the first DNA level addition. Testing shows up to a 17x reduction in static levels when StatBlock™ is introduced into the synthetic turf fibers.
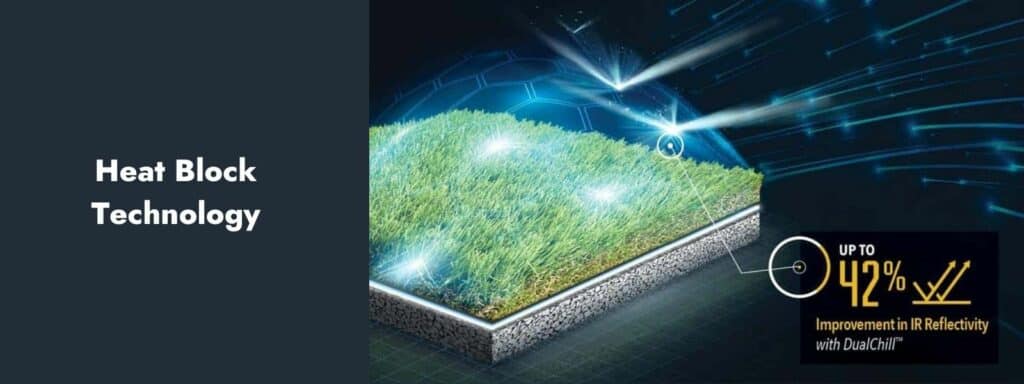
Heat Blocking Technology
Lowering the surface temperature of artificial turf has been an ongoing battle throughout the turf industry for years. While synthetic grass doesn’t retain heat like pavement, asphalt, bricks, or pavers, it certainly doesn’t stay as cool as natural grass. To help cool their turf products, several companies have introduced technologies that deflect UV rays, thereby preventing the buildup of heat.
- TurfHub’s “CoolFlo”
- SYNLawn’s “DualChill™”
- SGW’s “TigerCool”
Attempts to keep turf surfaces cool extend beyond the turf fibers. Several infill products have been introduced to help combat the “Artificial Turf Heat Issue.” The infill materials work much differently than the UV-reflective turf fibers. They work by absorbing water and moisture from rain, irrigation, morning dew, etc., and then slowly releasing it.
The process is known as “Evaporative Cooling” and it cools the turf in the same way our evaporating sweat cools us. Two of the most prominent cooling infills are T°Cool™ Infill and HydroChill Infill. They claim that their infills help lower the surface temperature of artificial turf by 30°F to 50°F.
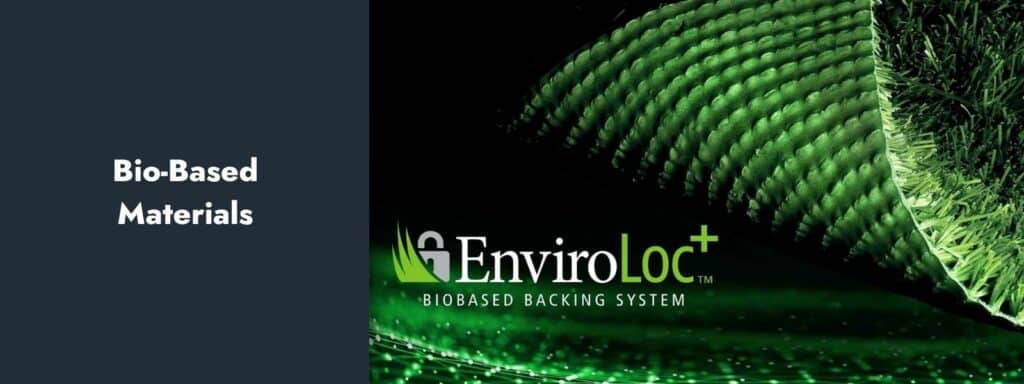
Bio-Based Materials
SYNLawn’s exclusive EnviroLoc+™ Backing System is an environmentally friendly, multi-layer component system that “locks” in durable turf fibers, extending the product’s life cycle. Made in the USA, the EnviroLoc+ Backing System replaces a large portion of petroleum-based polymers with biobased polymers created from sustainable resources including soybean oil from American farmers.
The system is created with a durable 2-part woven (Polypropylene and Polyester) backing for a fuller tufted look. This is thought to result in less fiber loss for a more environmentally responsible approach to synthetic grass. The long life expectancy of SYNLawn’s artificial grass reduces the impact on landfills, eliminates emissions from lawn care tools, and saves precious water resources.
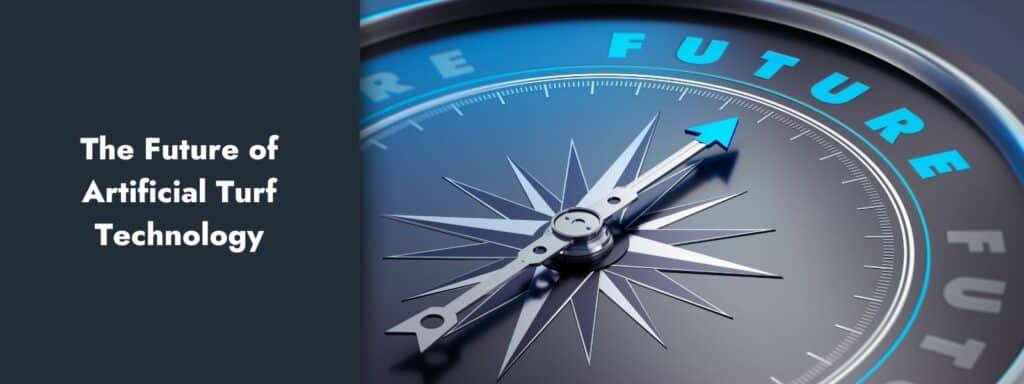
The Future of Artificial Turf Technology
The future of artificial turf is set to be shaped by several key advancements in technology and materials, driving growth and adoption of synthetic playing surfaces. Innovations in materials, sustainability, and maintenance will play a crucial role in shaping the future landscape of artificial turf.
Enhanced Durability & Improved Safety
Future artificial turf systems are expected to be even more durable, with longer lifespans and reduced wear and tear. This will lead to cost savings for sports facilities and organizations, as well as a more consistent playing surface for athletes.
Ongoing research and development will prioritize making artificial turf even safer for athletes. This includes efforts to reduce the risk of injuries associated with playing on artificial surfaces, such as addressing issues related to traction and impact absorption.
Non-Infill Systems
TenCate Grass has been collaborating with sport clubs, athletes, and partners since 2009 to develop non-fill turf, which closely resembles natural grass in player experience and appearance. Non-fill turf does not contain performance infill. Instead, it has a dense layer of texturized thatch fibers at the bottom to support the fibers and absorb impacts. It would solve issues surrounding infill, such as infill splash, transportation, and maintenance requirements.
Increased Sustainability
Turf Manufacturers are actively exploring sustainable materials and practices to minimize the environmental impact of artificial turf. This includes the use of recycled materials in turf construction and developing eco-friendly maintenance practices.
Manufacturers are likely to increasingly use recycled materials in the production of artificial turf, including recycled plastics and rubber. This not only reduces waste but also decreases the demand for new raw materials, contributing to a circular economy. Efforts to design turf components that are easily recyclable at the end of their lifespan will become more prevalent. This ensures that old turf can be repurposed into new products, reducing waste in landfills.
The development and adoption of infill materials that are more environmentally friendly, such as cork or coconut-based infill, will continue. These materials are biodegradable and have a lower carbon footprint compared to traditional infills like rubber.
By researching innovative materials and technologies, the future of artificial turf aims to strike a balance between performance and sustainability, making it a more eco-friendly choice for various applications.
Smart Turf
Future versions of artificial turf are expected to integrate sensors and other advanced technologies to enhance functionality and user experience. These innovations will include the incorporation of embedded sensors that can monitor various parameters such as temperature, moisture levels, and even player performance metrics in real-time. Such data can be utilized for efficient turf maintenance, monitoring infill levels, and improved athlete training and safety.
Smart technologies may enable interactive features such as augmented reality (AR) gaming, responsive lighting systems, or even dynamic playing surface adjustments based on different sports or weather conditions. These advancements will not only make artificial turf more versatile but also contribute to its role as a cutting-edge technology in sports and recreational settings.
Overall, the future of artificial turf holds great promise, with advancements in durability, player safety, sustainability, and the integration of smart technologies set to transform the landscape of synthetic playing surfaces. Researchers and manufacturers are constantly innovating to further improve the performance, sustainability, and versatility of synthetic grass. The possibilities are endless, from improved recycling processes to enhanced wear resistance.
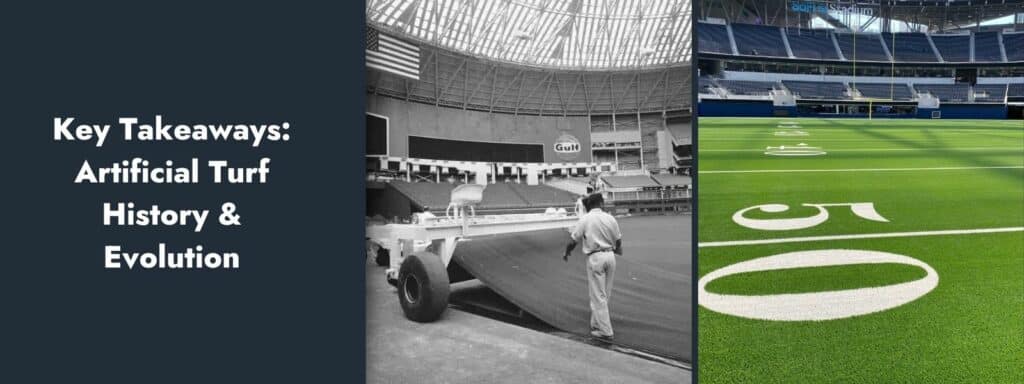
Key Takeaways: Artificial Turf History & Evolution
From its early days as Astroturf® to the sophisticated synthetic grass we see today, artificial turf history and evolution has been nothing short of remarkable. Advancements in materials, manufacturing technology, and environmental considerations have turned synthetic grass into a sustainable, versatile, and safe option for a wide range of residential and commercial applications.
As we look to the future, the possibilities for artificial turf technology are limitless, promising even more exciting developments in the years to come. Whether it’s for sports, landscaping, or residential use, artificial turf has truly transformed our green spaces.
If you’re considering artificial grass for your home, business, or organization, then you’ve come to the right place! Browse the Turf Network’s artificial turf information hub to learn all you want about artificial turf. Once comfortable with your knowledge, use our directory to search for an artificial turf installer, supplier, or manufacturer near you!
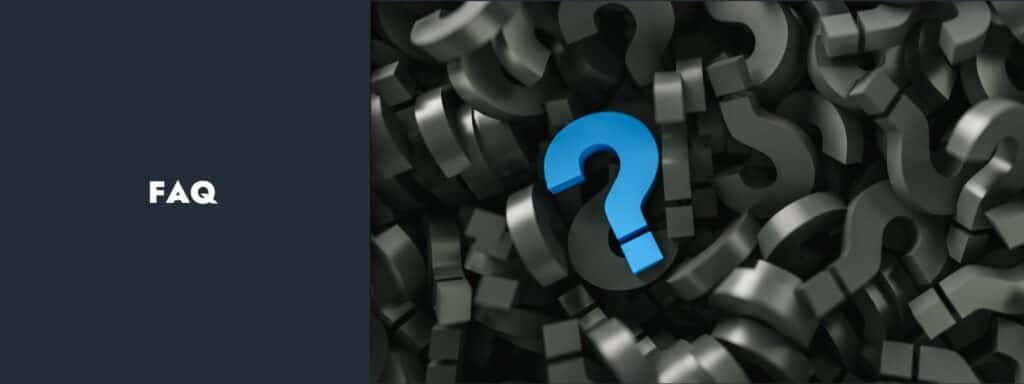
FAQs (Frequently Asked Questions)
Is Artificial Turf Environmentally Friendly?
Yes, artificial turf has become more eco-friendly over the years. Many turf manufacturers use recycled materials, and synthetic grass significantly reduces water consumption compared to natural grass. It also eliminates the need for gas-powered landscaping equipment like lawnmowers, which emit more carbon dioxide than cars. Another important environmental benefit of synthetic grass is the elimination of potentially harmful chemicals like fertilizers and pesticides used on natural grass. Those chemicals make their way into sewers, streams, and groundwater.
Is Artificial Turf Suitable for Sports Fields?
Absolutely! Artificial turf is commonly used in sports fields due to its durability, consistent playing surface, and customization options for different sports. The suitability of artificial turf for sports fields is evidenced by its widespread adoption by sports teams, colleges, universities, high schools, etc. Its popularity as a ground cover for playgrounds and children’s play areas is indicative of the safety and efficacy of synthetic grass as a ground cover.
How Long Does Artificial Turf Last?
The lifespan of artificial turf varies depending on factors like usage and maintenance. Most sports field turf manufacturers, like FieldTurf, claim that their sports field systems last 8 to 12 years. For applications with less usage and foot traffic, synthetic grass can last up to 15-25+ years with proper maintenance and care.
Can I Install Artificial Turf Myself (DIY)?
Technically, Yes. However, DIY installations are not recommended for most turf installations. Properly installing artificial turf requires specialized equipment and more importantly, experience. We strongly recommend hiring professionals for the best results.
A proper artificial turf installation process ensures longevity and optimal performance. DIY installations often need to be redone by a professional turf installer to fix mistakes made during the initial installation. Below are a few of the most common errors found in DIY turf installations:
- Wrinkles in Turf
- Indentations/Dips/Divots in the Turf
- Seam Separation
- Loose/Unsecure Edges
- Water Pooling/Flooding